Corrosion in boilers? Be aware of the main causes
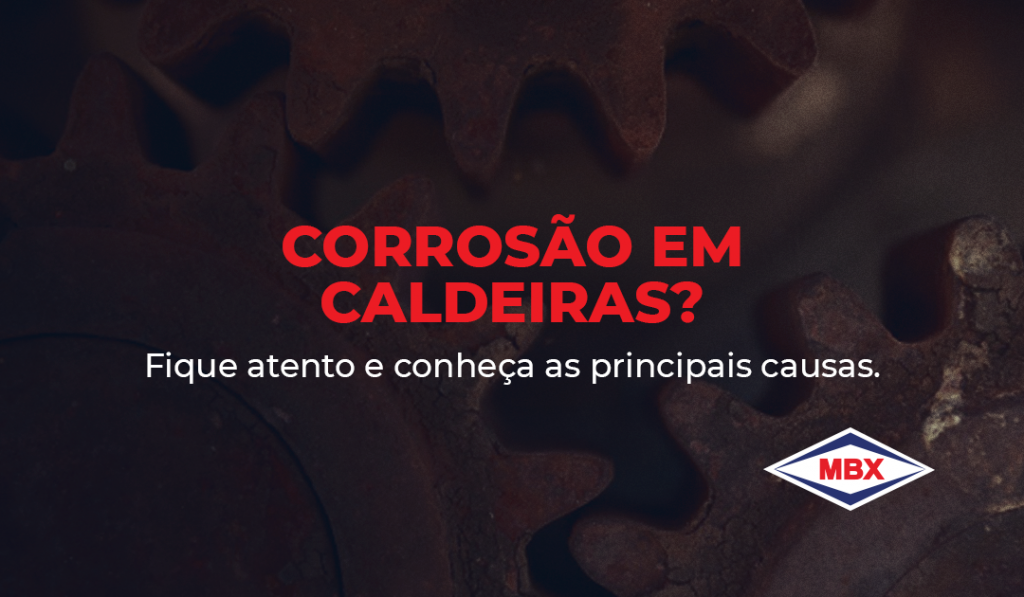
Boilers are widely used equipment in industries. They work under high pressure and high temperatures, so Any problem needs to be quickly identified and corrected . One of the most common is corrosion in boilers.
It is a natural problem, regardless of the type and usability of the equipment, but in some cases it can cause serious damage. Therefore, it is essential to know what the most common causes are and what preventive measures should be taken to reduce the consequences of this problem.
See what the main causes of corrosion in boilers are and learn what preventive measures are to avoid its occurrence.
Most common types of corrosion in boilers
Corrosion usually occurs “silently” and is not detectable by the boiler’s operating instruments (safety valves and pressure switches), as it is not necessarily accompanied by an increase in operating pressure.
Some of the main causes of corrosion in boilers are:
- acidic pH;
- Presence of suspended solids;
- Copper and nickel;
- dissolved oxygen;
- Elevation of sodium hydroxide and chlorides, among others.
Thus, in general, corrosion in boilers can occur in the following ways:
Iron oxidation – This is one of the most common causes of corrosion. Boilers are mainly made of carbon steel, which is sensitive to the action of water and, if subjected to high temperatures, can occur frequently.
Sometimes, the magnetite film prevents corrosion from occurring in the boiler in a short period of time. However, when there are thermal shocks and expansions at the edges of the tubes, this magnetite layer disappears, initiating the iron oxidation process.
Caustic brittleness (or alkali cracking) – Occurs when sodium hydroxide (caustic soda), in high concentrations (above 5%), migrates to cracks or other places where there is no longer a protective magnetite film, thus reacting directly with the iron.
This type of corrosion is called caustic brittleness, or alkali cracking.
Salt corrosion – Chlorides accelerate the corrosion process in boilers, as they tend to migrate to regions where there is no magnetite, triggering the problem.
There is also the issue of hydrolysis of magnesium chloride, which turns into hydrochloric acid and affects the steel of the boiler components.
Corrosion by dissolved gases – Chemical reactions can produce substances that can reach the boiler structures and accelerate the corrosion process. One of these substances is iron sulfide, which is a product of the reaction of hydrogen sulfide with sodium sulfite, used in water treatment.
Carbon dioxide is another element that can also cause problems for boilers, as water, in contact with gas, leaves the liquid acidified and, as a consequence, pits form.
How to avoid further damage from corrosion
Corrosion in boilers is a problem that becomes unavoidable under some circumstances, so the best way to reduce its severity is prevention and treatment of boiler feed water.
The industry has at its disposal different types of water treatments that are used in boilers and that control the corrosive process. See below:
- External treatments of feed water through its clarification with suitable agents and equipment:
This type of treatment includes the removal of turbidity, color and gases; removal of iron, manganese and hardness; demineralization; removal of gases.
- Internal treatments:
This type of treatment involves the chemical removal of oxygen through deaeration with sodium sulfite, hydrazine and the neutralization of carbon dioxide.
In low and medium pressure boilers, treatments can be based on precipitant – phosphate plus polyelectrolyte; complexometric; mixed and dispersant.
As for high pressure boilers, we must work with demineralized and condensed water, recovered with maximum purity.
Even boilers that are out of operation need to be protected against corrosion. To achieve this, it is recommended to use deaerated water with activated hydrazine or catalyzed sodium sulfite. Inactive boilers can have wet or dry protection.
Take advantage and see what the main measures to keep your boiler working properly .