Step by step: Understand the boiler concentration and purge cycle
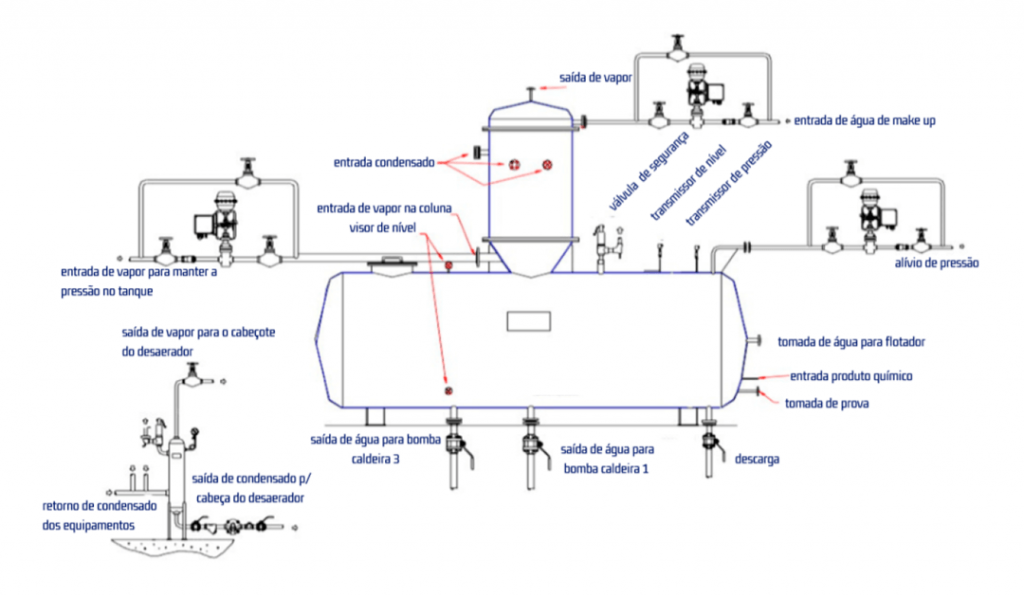
Here on our blog we have already discussed several topics related to all types of boilers . However, in today's article we have chosen to address a slightly different topic that usually receives little attention: the concentration cycle and the purge discharge rate in cooling systems.
But after all, what is the boiler concentration cycle and how important is it for the operational process of a boiler that influences the quality of the water used?
Concentration cycle in boilers: What does it mean?
In general, even with excellent treatment, boiler feed water will always contain minerals and many other molecules in its composition (Cl-, Mg2+, Ca2+, Fe2+, Si4+, among others), known as impurities.
What happens, however, is that as the boiler starts generating steam – with the pure water turning into a gaseous state – these impurities tend not to evaporate, remaining inside the boiler. With the entry of more water and continuous generation of steam, the concentration increases.
This entire process is called the Concentration Cycle, with the “concentrated water” inside the boiler commonly being called “sludge”.
In a more technical explanation, the concentration cycle is the ratio between the concentration of a given ion in the system (in the tower or in the boiler), divided by the concentration of this same ion in the system feed.
Still having trouble? Here’s a practical example:
Imagine a cooling tower that has a concentration of 100 ppm of sulfate and that the makeup water used for this tower contains a sulfate content of 20 ppm. Thus, we will have 5 cycles (division of 100/20 = 5 cycles), that is, the water in the cooling tower is 5 times more concentrated than the makeup water for this scenario.
Why is the concentration cycle so important for a boiler?
The concentration cycle represents an essential process for the boiler, being responsible for the following results:
- Raise the pH of the water inside the boiler;
- Minimize the corrosion process and avoid silica scaling by passivation;
- It helps to decrease the amount of dissolved O2 in the boiler, which also helps to minimize the corrosion process of the pressure vessel.
Furthermore, during the concentration process, the amount of dissolved solids (TDS, measured in ppm) will also increase, which increases the electrical conductivity of the water inside the boiler.
Therefore, it is important to understand that there is an ideal TDS value and this depends on the type of boiler and the operation. As a reference, for common fire tube boilers, the ideal is to work with water between 4,000 and 5,000 microns/cm.
This is essential because when the boiler operates with conductivity below the reference value, the pH will probably also be low. When the conductivity is higher, the problem of moisture being carried along with the steam may occur, damaging the quality and causing problems such as water hammer.
Boiler blowdown reduction: ideal for reducing “concentrated water”
As we have seen, the water consumption of a boiler is a function directly related to the concentration cycle of this equipment. Thus, when the recirculation flow and the thermal load are kept constant, it is possible to imagine that increasing the concentration cycle will imply less purging and consequently water savings.
One of the most sophisticated ways to control boiler TDS levels is to automate the purge process.
In the boiler, bottom purges are essential to maintain the concentration of dissolved solids in the water within control limits and avoid corrosion/water carryover problems into the steam.
In this scenario, the most effective ways to ensure boiler operation with a minimum amount of purges (and consequently maximum concentration cycle value) are:
- Adequate pre-treatment of makeup water;
- Maximum use of condensate, thus improving the quality of the feed water;
- Use of appropriate chemical products in maintenance treatment.
Finally, this entire concept will help industries guide choices and projects that aim to save water, reducing the total operating cost of treating feed water.
To find out everything about boilers and their accessories, we invite you to visit MBX blog .