See how to avoid problems and wear in boilers
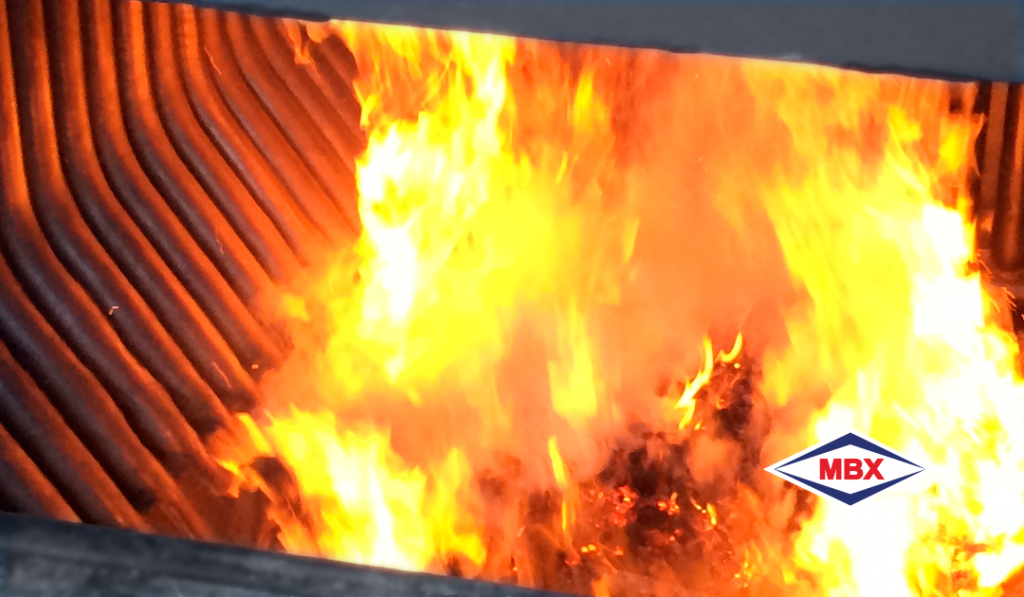
Boilers are equipment used to generate steam used in various industrial processes. However, boilers are subject to various risks when they do not receive due care in terms of use and maintenance.
These boilers are responsible for producing and accumulating steam always under pressure higher than atmospheric pressure, therefore having a maximum pressure limit supported during operation.
However, the quality of this operation can be affected by several problems and wear and tear that can cause the equipment to stop or even cause large-scale explosions, as we mentioned in this article .
Check out the main causes of problems and wear in boilers, as well as some essential tips for keeping this equipment working properly. Follow along!
Most common causes of boiler failures and problems
When there is no proper care and maintenance, any boiler can present faults and problems that can compromise its operation and, in more serious cases, even cause serious damage to the equipment and the health of the operator.
Among these flaws, it is important to mention:
-
Corrosion
In boilers, corrosion is a natural problem represented by the reduction in the thickness of the boiler surfaces subjected to pressure . Therefore, it is one of the main causes of the degradation of this equipment.
The corrosive process of boiler parts can occur in several ways, such as: internal corrosion, generalized oxidation of iron, galvanic corrosion, corrosion by differential aeration, saline corrosion, among many others.
Unfortunately, corrosion is one of the most difficult factors to identify, as it can occur internally and not be accompanied by an increase in pressure during work.
-
Water or steam leak
In boilers, water leaks and steam leaks are very common defects in boilers. The causes are varied, including:
- Damaged or stuck valve seats;
- Poorly positioned cover or flange gasket;
- Cracked or punctured pipe;
- Overheating followed by rapid cooling, causing the tubes to come loose from the mirrors.
In addition to leaks, carryover is another important boiler villain. This is a phenomenon characterized by the carryover of water from the boiler to the steam line, causing several inconveniences, such as the formation of deposits in superheaters and valves and a drop in the performance of equipment that uses steam for heating.
-
Pressure increase
This failure is one of the most serious occurrences and therefore needs to be avoided, since increased pressure is one of the main reasons for boiler explosions.
It is worth noting that the internal pressure of the boiler will increase due to a series of factors, operational or otherwise, such as mechanical failures, problems with safety valves (more serious) and even defects during the manufacture of industrial boilers.
-
Lack of water
For boilers to always work well, it is extremely important that the steel remains in contact with water at all times, so that it can stay cool.
If the water does not reach a certain location for a while, overheating will occur, reducing the resistance of the equipment walls. Furthermore, when the supply system fails and causes a lack of water in the boiler, the tubes tend to overheat, resulting in rupture.
-
Forced operation
Boilers in operation are designed to have enough power to meet a specific demand. However, when they are forced to work harder and generate more heat, the consequence can be overheating in several of their parts, deforming them or even causing the equipment to completely break down.
How to avoid problems and wear on your boiler?
It doesn't matter if the fault that occurs in boilers is simple or very complex, the ideal is to always prevent this problem from occurring. For the equipment to always work efficiently and safely, some actions must be prioritized.
The first step to avoid accidents due to excess pressure is to operate at a pressure lower than the maximum allowable working pressure (PMTA) stated on the chair's plate.
To identify the operating pressure, there are several instruments that can be installed. NR -13 requires that the boiler be equipped with an instrument that indicates the accumulated steam pressure, known as a pressure gauge. It also requires a safety valve adjusted for heat equal to or less than PMTA.
Another important action to avoid failures is to keep up to date with regular inspections, which allow monitoring of material wear and possible corrective maintenance.
Finally, it is up to the industry to keep the instruments calibrated and in working order, as well as to keep the operating personnel trained to, in addition to operating the boiler correctly, be able to identify possible faults.
Enjoy this article and understand why you should have pay attention to the main causes of corrosion in boilers .