Understand the NR 13 standard and its importance
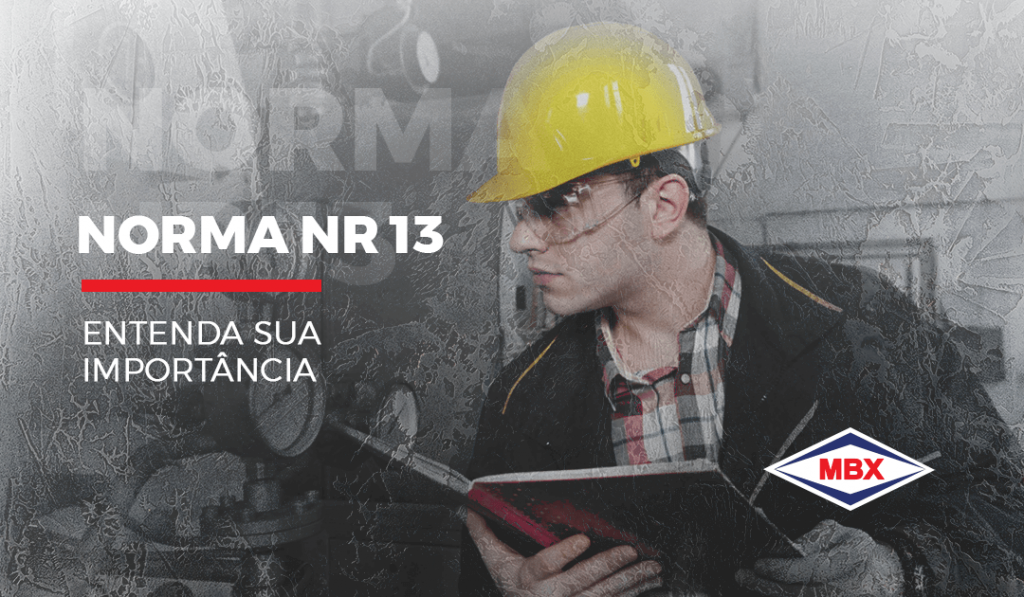
Pressure vessels, boilers and interconnecting pipes are essential for many industrial processes involving the use of fluids or gases. Such equipment must be designed to safely withstand high internal pressures. Therefore, when operating this equipment, it is essential to know Standard NR 13 .
Characterized as Regulatory Standard No. 13 – Boilers, Pressure Vessels and Pipes , standard NR 13 aims to condition the safety inspection and operation of pressure vessels, boilers and pipes.
Do you want to know everything about this standard? Then keep reading the content. In it, we will present the main objectives of this standard that primarily aims at the safety and health of workers.
What is NR 13?
Standard NR 13 is one of the regulatory standards created and regulated by the Ministry of Labor and Employment, its full name is Regulatory Standard No. 13 – Boilers, Pressure Vessels and Pipes .
This standard was approved by Ordinance No. 3,214 of June 8, 1978, but since then it has undergone several revisions and adaptations that aimed to follow and align with the technological developments of this equipment.
The first revision of NR 13 occurred in May 1984, followed by another in December 1994, and a third update in June 2008. Another revision was made in 2014. The last and most recent update occurred in September 2017.
Basically, this regulatory standard establishes minimum requirements for managing the integrity of boilers, pressure vessels and their respective interconnecting pipes in aspects related to installation, inspection, operation and maintenance, always aiming at the safety and health of workers.
Pressure vessels and boilers: what are they according to NR 13?
Standard NR 13 presents the general provisions on what are Pressure Vessels and what are Boilers.
According to this standard, pressure vessels are equipment that contain fluids under internal or external pressure, different from atmospheric pressure. Such pressure vessels are classified into categories according to the fluid class (Class A to Class D) and the risk potential (based on the product PV, where P is the maximum operating pressure in MPa, in module, and V is its volume in m³).
Boilers are classified according to standard NR 13 as equipment designed to produce and accumulate steam under pressure greater than atmospheric pressure, using any energy source, designed in accordance with relevant codes, with the exception of reboilers and similar equipment.
For the purposes of this NR, boilers are classified into 2 (two) categories:
- Category A boilers: whose operating pressure is equal to or greater than 1960 kPa (19.98 kgf/cm²), with a volume greater than 50 L (fifty liters);
- Category B boilers: whose operating pressure is greater than 60 kPa (0.61 kgf/cm²) and less than 1960 kPa (19.98 kgf/cm²), internal volume greater than 50 L (fifty liters) and the product between the operating pressure in kPa and the internal volume in m³ is greater than 6 (six).
Safety items for pressure vessels and boilers
To ensure the integrity of the equipment and the health of the worker, Standard NR 13 states that boilers and pressure vessels must have several safety items.
For pressure vessels:
– Safety valve or other safety device with opening pressure adjusted to a value equal to or lower than the PMTA (Maximum Allowable Working Pressure);
– Pressure vessels subjected to vacuum must be equipped with vacuum-breaking safety devices or other means provided for in the design;
– Physical device or seal with warning signage to prevent blocking of the safety valve or other safety device;
– Instrument that indicates the operating pressure, installed directly on the vessel or in the system that contains it.
For boilers:
– Safety valve with opening pressure adjusted to a value equal to or lower than PMTA;
– Instrument that indicates the pressure of accumulated steam;
– Injector or water supply system independent of the main one that prevents overheating due to deficient supply, above design temperatures, of non-atomized solid fuel boilers or those burning in suspension;
– Dedicated system for rapid water drainage in alkali recovery boilers, with automatic actions after activation by the operator;
– Automatic water level control system with interlocking that prevents overheating due to poor power supply.
In addition to these items, both pressure vessels and boilers must have an identification plate affixed to their body, in an easily accessible and clearly visible location, with the following information:
– Name of the manufacturer; order number given by the boiler manufacturer; year of manufacture; maximum permissible working pressure; manufacturing hydrostatic test pressure; steam production capacity; heating surface area; design code and year of issue.
Hydrostatic Tests in the manufacture of boilers and pressure vessels
Among several other requirements, the latest update of Standard NR 13 (09/2017) also aims to regulate the testing and inspection periods for pressure vessels and boilers.
From this update onwards, hydrostatic tests will be carried out in manufacturing evaluations, with the test pressure value being introduced on the nameplate of these machines.
But do you know what a hydrostatic test is?
Basically, Hydrostatic Testing is characterized as a process in which the components of a system, such as boilers and pressure vessels, are tested for resistance and leaks by filling the equipment with a pressurized liquid.
The Hydrostatic Test aims to identify:
- Existing flaws in the material;
- Stress corrosion cracking and real mechanical properties; and
- Locate hard spots that could cause failure in the presence of hydrogen.
To read more content like this, access the our blog and happy reading!