Learn about the types of industrial sealing gaskets
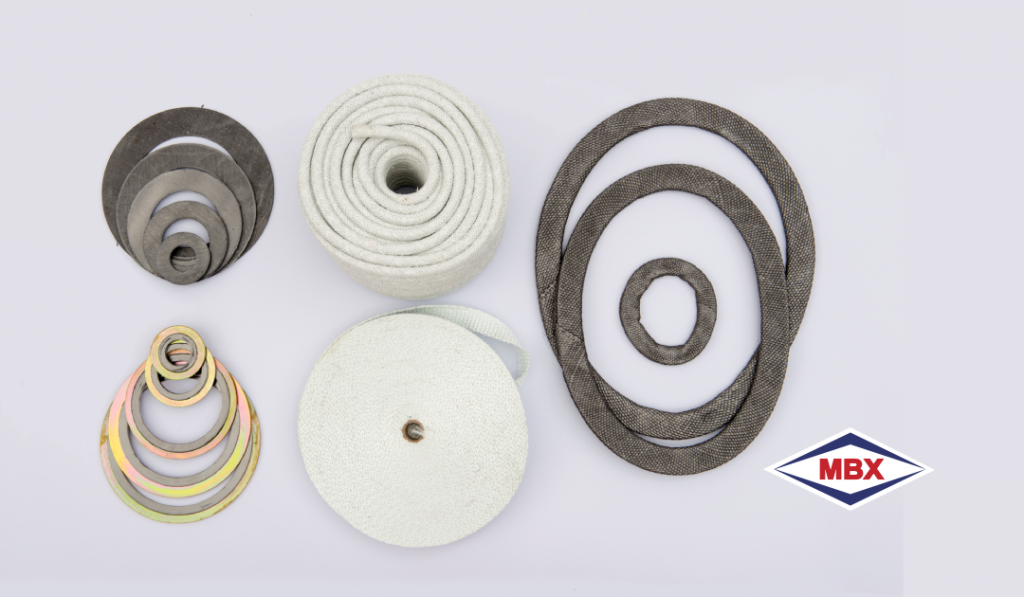
Widely used in machinery of all kinds, industrial sealing gaskets are essential components for providing greater safety and optimizing various procedures carried out in the industry.
However, even though it is a relatively simple component, many professionals do not know how industrial sealing works, nor that there are different types of sealing gaskets.
Therefore, it is worth knowing the main industrial sealing gaskets and which are the most suitable for each need, check it out:
What are industrial sealing gaskets?
In industries, the adoption of a industrial sealing system It is essential for several segments. The function of this device is to prevent solid, liquid or gaseous fluids from passing from the external to the internal environment.
This type of sealing helps to prevent contamination of the environment, in addition to preventing damage that could impair the functioning of machines and equipment. It also prevents the occurrence of wear, failures or errors that hinder industrial production.
Industrial sealing is made from a wide range of materials, following strict quality standards defined by national and international organizations. This is precisely why there are specific types of sealing gaskets for each need.
Main types of industrial sealing gaskets
One mistake that should never happen in the industrial sector is choosing the wrong industrial sealing gasket. If this happens, there is a possibility of leaks and failures between the surfaces and flanges, compromising the results and safety of the activity.
To avoid this, you need to choose the best sealing gasket. Check out the 3 types of industrial sealing gaskets most commonly used in the industrial sector below:
Hydraulic Cardboard
This type of sealing gasket is the most widely used in the industrial sector, mainly because it is cheaper. It is made from NBR (nitrile) rubber and mixed with different types of fibers. These models are made from combinations of fibers, elastomers and additives.
These compositions result in materials with different characteristics that cover many applications. Below, four varieties of hydraulic cardboard gaskets will be presented.
- Inorganic fiber gaskets – They have high thermal stability, being indicated for the manufacture of sealing joints and used for high temperature and pressure services. They also have high chemical resistance, making them compatible with many chemical products.
- Asbestos hydraulic cardboard gaskets – are most commonly used in pipe or equipment flanges, as they withstand higher temperatures and pressure levels.
- Cellulose hydraulic cardboard gaskets – They are manufactured from cellulose fibers, NBR nitrile rubber and reinforcing fillers. In addition, they are asbestos-free and can withstand temperatures of 210ºC and 50 bar of maximum pressure. Their greatest attraction is the fact that they are low cost.
- Aramid fiber hydraulic cardboard gaskets – are made of NBR nitrile rubber and reinforcing filler, allowing them to withstand temperatures of 400ºC and 110 bar of maximum pressure. They offer excellent cost-benefit and are widely sold on the market.
PTFE (polytetrafluoroethylene)
PTFE products stand out for being inert, non-toxic and resistant to misfortunes, making them compatible with most fluids, serving the most varied industrial segments.
This type of industrial sealing gasket has high chemical resistance, meeting all pH ranges (0 to 14) without causing contamination. Due to this characteristic, it is recommended for high-performance sealing in which fluid leaks cannot occur under any circumstances.
Another highlight of the PTFE industrial sealing gasket is that it can be used on any type of flange. Furthermore, exposure to water does not pose a risk, as does use in a corrosive environment.
Among the main advantages of PTFE are:
- Greater sealability;
- Easy to install;
- Free of asbestos and graphite;
- Highly compressible
- Non-toxicity;
- Excellent chemical resistance.
Flexible Graphite
Flexible graphite sealing gaskets are the safest for severe service conditions. They are manufactured from the expansion and calendering of pure natural graphite (95% to 99% purity). They tend to have greater sealability than others because they are resistant to temperature fluctuations, with high chemical resistance and thermal and electrical conductivity.
The main point of attention is that in oxidizing atmospheres and in conditions above 450ºC, use requires a more detailed analysis, mainly because they are the most expensive among the options.
Did you enjoy learning more about the main industrial sealing gaskets? Then Learn more about the MBX Blog