Industrial boilers: Know their main types
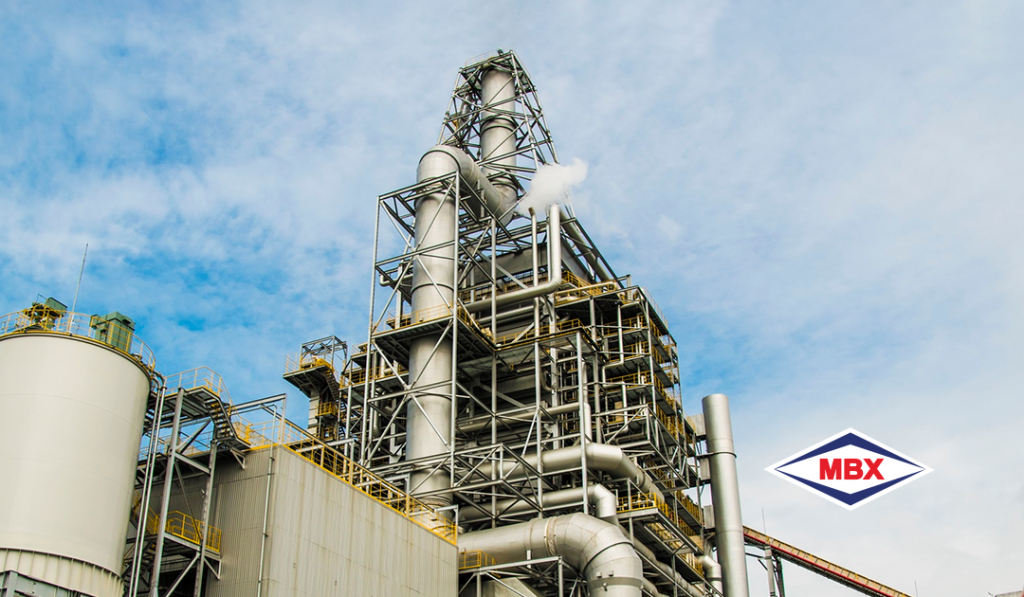
Every large industry uses a variety of equipment with different construction aspects and objectives. Among them, industrial boilers are essential, as they are responsible for producing and accumulating steam for many needs.
By definition present in NR13, industrial steam boilers “ are equipment designed to produce and accumulate steam under pressure higher than atmospheric pressure, using any energy source, designed in accordance with relevant codes, with the exception of reboilers and similar equipment ”.
In terms of construction, boilers can be classified into a number of types that have evolved over time, since the first Industrial Revolution. Based on this, it is important to know the main types of industrial boilers, as well as the differences between them during operation.
Main types of industrial boilers
Industrial boilers currently used in the industrial sector can be divided into two large groups, each with respective subdivisions:
- Fire tube boilers
- Water tube boilers.
Thus, based on the positions of the tubes, the positioning of the furnace, and other construction aspects, the main types of boiler are divided as follows:
Fire tube boilers
Industrial fire tube boilers are those in which smoke and gases resulting from combustion pass through the tubes, heating them. Water passes around these tubes. As a result, the heat from the metal is transferred to the water, heating it and generating steam.
The diagram below represents the fire tube method of generating steam:
These boilers can generate 100 to 30 thousand kg/h, with pressure of up to 30 kgf/cm2. On the other hand, they have simple construction, making them ideal for industries that require a standard amount of energy.
Fire tube boilers can be vertical or horizontal:
In vertical fire tube boilers, the tubes are installed vertically in a cylindrical body closed at the ends by plates, known as mirrors. The internal furnace is located in the cylindrical body just below the lower mirror.
Horizontal fire tube boilers have internal pipes arranged horizontally, through which hot gases pass. They can have 1 or 2 gas passes in the steam drum.
Water tube boilers
With operation and construction pattern opposite to fire tube boilers, water tube boilers have water present inside the tubes so that they are heated, and are surrounded by gases resulting from combustion, as represented in the diagram below:
In this specific boiler, the heat resulting from combustion passes around the tubes, heating them. The tubes transfer the heat to the water in them, heating it and generating steam.
Due to their construction and design characteristics, water tube industrial boilers are normally used in applications that require very high pressure, above 21 barg (category A of NR 13), both for generating saturated and superheated steam.
Precisely for this reason, water tube boilers are generally adopted in modern industrial projects, such as hydroelectric plants, as they have the capacity to produce large quantities of steam at high pressures and temperatures. Steam production in these types of boilers, for example, has the potential to reach more than 500 tons/h.
Due to these greater demands, these boilers require a much more complex construction design. It also requires that the feed water be treated with much more care.
Mixed boilers
There is also a third variation of industrial boilers. It has a mixed (hybrid) characteristic, that is, it is fire tube and water tube.
Water tubes pass through the furnace of this type of boiler, indicating the water-tube part. The exhaust gases then travel through tubes to the fire-tube part, and from there they exit through the chimney.
The diagram below represents this constructive form well:
Prevention and Maintenance: Essential for the proper functioning of industrial boilers
As they are equipment that always operate under high pressure and high temperatures, boilers are not simple equipment and if poorly handled, they can cause problems during operation , such as failures and wear that have the potential to cause serious accidents.
Therefore, it is up to the industry to adopt preventive and maintenance measures to keep the equipment working properly. Thus, it is essential to keep up to date with regular inspections of the equipment, which allow monitoring of boiler wear and possible corrective maintenance.
It is also important that the industry maintains equipment complementary to the boiler with superior quality, such as industrial seals and safety valves that guarantee the proper functioning of this industrial steam generator.
No less important, there is a need for the industry to have professionals who are always qualified and have proven experience to operate and carry out maintenance on industrial boilers.
Now that you know the main types of boilers, we invite you to explore the MBX Blog