Comprender la norma NR 13 y su importancia
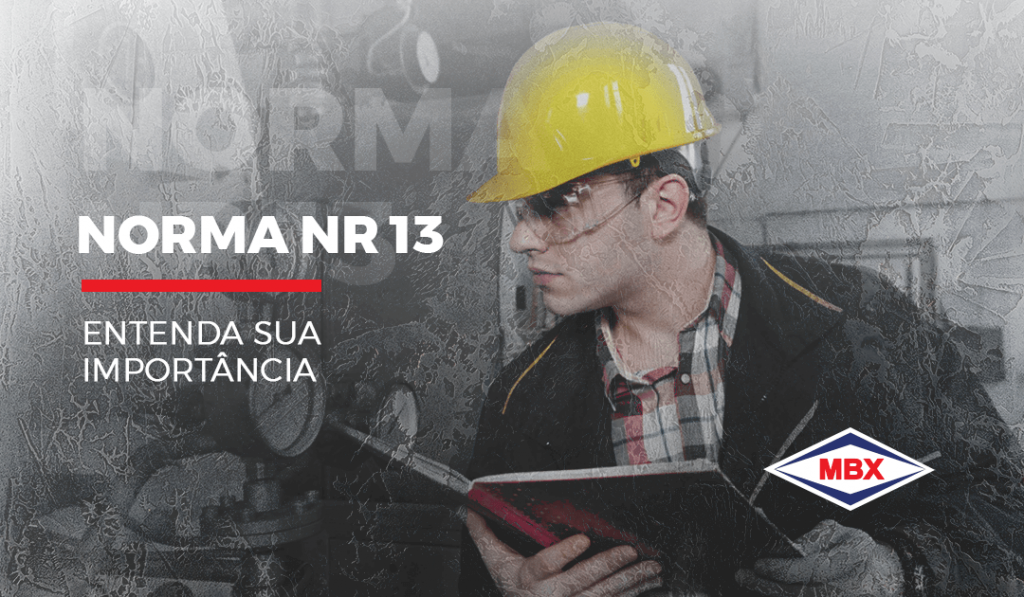
Los recipientes a presión, las calderas y las tuberías de interconexión son esenciales para muchos procesos industriales que implican el uso de fluidos o gases. Dichos equipos deben diseñarse para soportar con seguridad altas presiones internas. Por lo tanto, al operar este equipo, es fundamental conocer la Norma NR 13 .
Caracterizada como Norma Regulatoria N° 13 – Calderas, Recipientes a Presión y Tuberías , la norma NR 13 tiene como objetivo condicionar la inspección de seguridad y operación de recipientes a presión, calderas y tuberías.
¿Quieres saber todo sobre esta norma? Así que continúa leyendo el contenido. En él presentaremos los principales objetivos de esta norma, que apunta principalmente a la seguridad y salud de los trabajadores.
¿Qué es la norma NR 13?
La Norma NR 13 es una de las normas reglamentarias creadas y reguladas por el Ministerio de Trabajo y Empleo, su nombre completo es Norma Reglamentaria N° 13 – Calderas, Recipientes a Presión y Tuberías .
Esta norma fue aprobada por la Ordenanza nº 3.214 del 8 de junio de 1978, pero desde entonces pasó por varias revisiones y adaptaciones encaminadas a seguir y alinearse con los desarrollos tecnológicos en estos equipos.
La primera revisión de la norma NR 13 tuvo lugar en mayo de 1984, seguida de otra en diciembre de 1994, una tercera actualización tuvo lugar en junio de 2008. En 2014 hubo otra revisión. La última y más reciente actualización se produjo en septiembre de 2017.
Básicamente, esta norma reglamentaria establece requisitos mínimos para la gestión de la integridad de las calderas, recipientes a presión y sus respectivas tuberías de interconexión en aspectos relacionados con la instalación, inspección, operación y mantenimiento, buscando siempre la seguridad y salud de los trabajadores.
Recipientes a presión y calderas: ¿qué son según la NR 13?
La norma NR 13 presenta las disposiciones generales sobre qué son los recipientes a presión y qué son las calderas.
Según esta norma, los recipientes a presión son equipos que contienen fluidos bajo presión interna o externa, distinta a la presión atmosférica. Dichos recipientes a presión se clasifican en categorías según la clase de fluido (Clase A a Clase D) y el riesgo potencial (dependiendo del producto fotovoltaico, donde P es la presión máxima de funcionamiento en MPa, en módulo, y V es su volumen en m³ ).
Las calderas se clasifican según la norma NR 13 como equipos diseñados para producir y acumular vapor a presión superior a la atmosférica, utilizando cualquier fuente de energía, diseñados de acuerdo con los códigos pertinentes, excluyendo los rehervidores y similares.
Para efectos de esta NR, las calderas se clasifican en 2 (dos) categorías:
- Calderas de categoría A: cuya presión de funcionamiento sea igual o superior a 1960 kPa (19,98 kgf/cm²), con un volumen superior a 50 L (cincuenta litros);
- Calderas de categoría B: cuya presión de funcionamiento sea superior a 60 kPa (0,61 kgf/cm²) e inferior a 1960 kPa (19,98 kgf/cm²), volumen interno superior a 50 L (cincuenta litros) y el producto entre la presión de funcionamiento en kPa y el volumen interno en m³ es superior a 6 (seis).
Elementos de seguridad para recipientes a presión y calderas.
Para garantizar la integridad de los equipos y la salud de los trabajadores, la Norma NR 13 establece que las calderas y recipientes a presión deben contar con varios elementos de seguridad.
Para recipientes a presión:
– Válvula de seguridad u otro dispositivo de seguridad con presión de apertura regulada en un valor igual o inferior a la PMTA (Presión Máxima de Trabajo Permitida);
– Los recipientes a presión sometidos a vacío deberán estar equipados con dispositivos de seguridad rompedores de vacío u otros medios previstos en el proyecto;
– Dispositivo físico o sello con señales de advertencia para evitar el bloqueo de la válvula de seguridad u otro dispositivo de seguridad;
– Instrumento que indica la presión de funcionamiento, instalado directamente en el recipiente o en el sistema que lo contiene.
Para calderas:
– Válvula de seguridad con presión de apertura regulada en un valor igual o inferior a PMTA;
– Instrumento que indica la presión del vapor acumulado;
– Inyector o sistema de suministro de agua independiente del principal que previene el sobrecalentamiento por mal suministro, por encima de las temperaturas de diseño, de las calderas de combustibles sólidos no atomizados o que queman en suspensión;
– Sistema dedicado de drenaje rápido de agua en calderas de recuperación de álcalis, con acciones automáticas después de la activación por parte del operador;
– Sistema de control automático del nivel de agua con enclavamiento que evita el sobrecalentamiento por mal suministro.
Además de estos elementos, tanto los recipientes a presión como las calderas deberán llevar adherida a su cuerpo, en un lugar de fácil acceso y claramente visible, una placa identificativa con la siguiente información:
– Nombre del fabricante; número de pedido indicado por el fabricante de la caldera; año de fabricación; presión de trabajo máxima permitida; presión de prueba hidrostática de fabricación; capacidad de producción de vapor; superficie de calefacción; código del proyecto y año de edición.
Ensayos hidrostáticos en la fabricación de calderas y recipientes a presión.
Entre otras exigencias, la última actualización de la Norma NR 13 (09/2017) también tiene como objetivo regular los períodos de prueba e inspección de recipientes a presión y calderas.
A partir de esta actualización se realizarán pruebas hidrostáticas en las evaluaciones de fabricación, introduciéndose el valor de la presión de prueba en la placa de características de esta maquinaria.
¿Pero sabes qué es una prueba hidrostática?
Básicamente, la Prueba Hidrostática se caracteriza por ser un proceso en el que se prueban los componentes de un sistema, como calderas y recipientes a presión, para comprobar resistencias y fugas llenando el equipo con un líquido presurizado.
La Prueba Hidrostática tiene como objetivo identificar:
- Defectos existentes en el material;
- Corrosión por tensión y propiedades mecánicas reales; y
- Localice los puntos duros que podrían causar fallas en presencia de hidrógeno.
Para leer más contenidos como este accede nuestro blog y feliz lectura!